Machining metal results in two products with value – a finished part and the waste (a.k.a swarf) that’s generated in the process.
At its most basic level, machining is taking a piece of metal or other material and removing some of it to create something of a particular shape, size and functionality. It’s considered a “subtractive manufacturing process” because it involves removing material to achieve a “final shape, size, or design” of a part or finished product.
Simple examples of machined parts include ball bearings, metal brackets and the pieces of a metal clutch for a truck.
The metal that’s removed – filings, fines, shavings and turnings – is debris or waste known collectively as “chips” or “swarf.” It usually winds up in a bin that’s part of a machinist’s workstation, and it’s generally recyclable.
While it can be recycled for use in other manufacturing processes, swarf often ends up being disposed of in landfills. However, there are companies who will pay you for your swarf scrap metal! In this blog post, we will discuss the types of swarf and how to recycle it for.
PROCESSES AND SWARF TYPES
Many individual processes in machining generate swarf, including boring, grinding, grooving, knurling, reaming, sawing, slotting and tapping. The three primary machining processes are drilling, milling and turning.
Drilling is the most common machining process – in fact, estimates suggest three-fourths of all metal removed in machining processes is the result of drilling. It’s usually done with a twist drill, with helical chips exiting through the grooves in the drill.
Milling machines use movable, rotating cutters for boring, creating slots, cutting gears and drilling holes. The process removes material from metals in a wide range of shapes and sizes, and on both flat and irregular surfaces.
Turning involves cutting with stationary blades applied to a piece of metal spinning on a lathe.
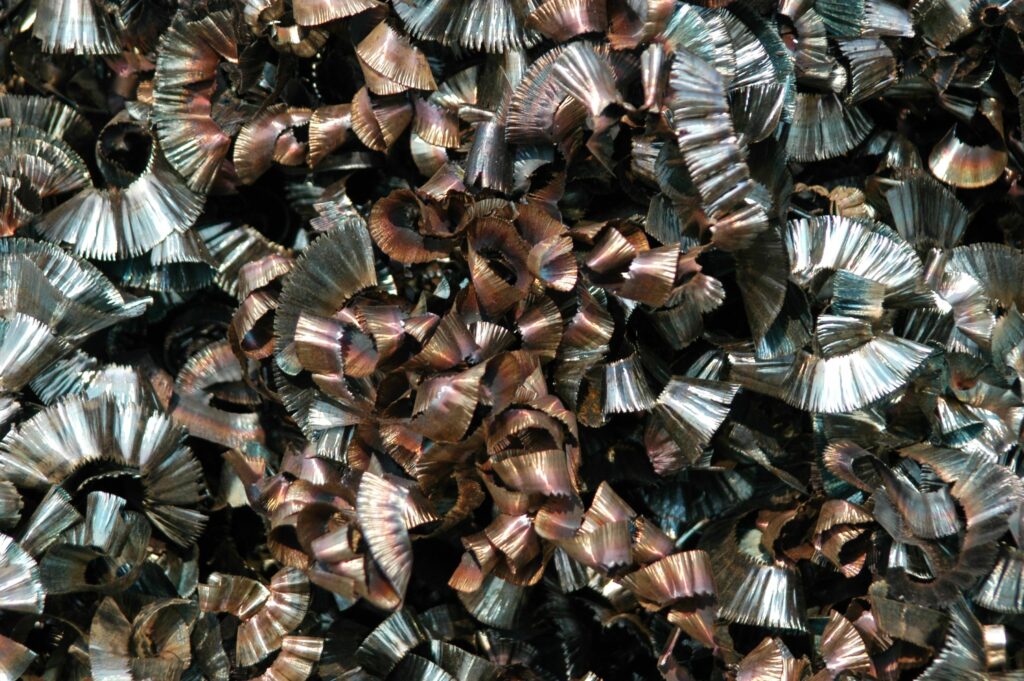
Machine shops put many different kinds of metals through these processes, including aluminum, brass, carbide, copper, iron, stainless steel, steel and tin. The processes described above generally result in one of several general categories of swarf.
Filings are tiny flecks, particles and slivers that most often result from grinding, filing or milling any number of metals.
Shavings can be anything from what resembles a powder up to larger chips sliced away from a piece of metal.
Turnings, as their names suggests, are the result of a turning process. Depending on the metal, they can look like curlicue pigs tails on their own, or when a bunch of them are together they can resemble a scrub pad used for washing dishes or scouring bathtubs.
HANDLE SWARF WITH CARE
Swarf can be dangerous, so the first rule of handling it is always wear gloves, protective clothing and safety glasses.
Tiny flecks and slivers of metal can get under your skin, into your eyes in powdery form or anywhere on your body as projectiles thrown from a machine. Extremely sharp edges on larger chips also can result in serious cuts or even loss of fingers.
In addition, swarf can contain reactive metals, which are highly flammable, and it’s often coated in oils used as coolants during machining operations. Make sure your shop and workstations are set up for fire prevention and equipped with extinguishers designed for metal fires.
GOOD REASONS TO RECYCLE SWARF
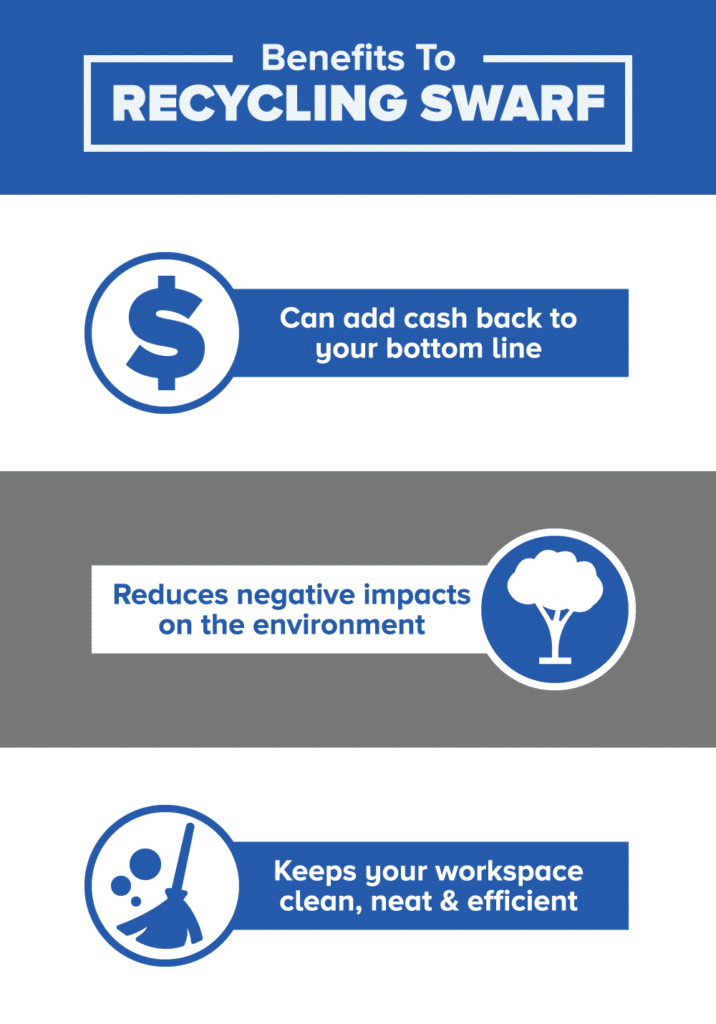
There are several great reasons to recycle your swarf. These are our favorites:
First, machining scrap is a resource for your business; you can sell it to a metal recycler like Cohen to put a little money back on your bottom line.
Next, recycling swarf, like recycling scrap metal in general, reduces negative impacts to the environment by avoiding toxic leaks from landfills, lowering carbon dioxide emissions and reducing demand for mining new ore.
And last but not least, establishing procedures for recycling swarf creates an excellent incentive for keeping your shop as clean, neat and efficient as possible.